Managing the microclimates of your supermarket: a guide to modern BAS solutions for evolving food retail spaces
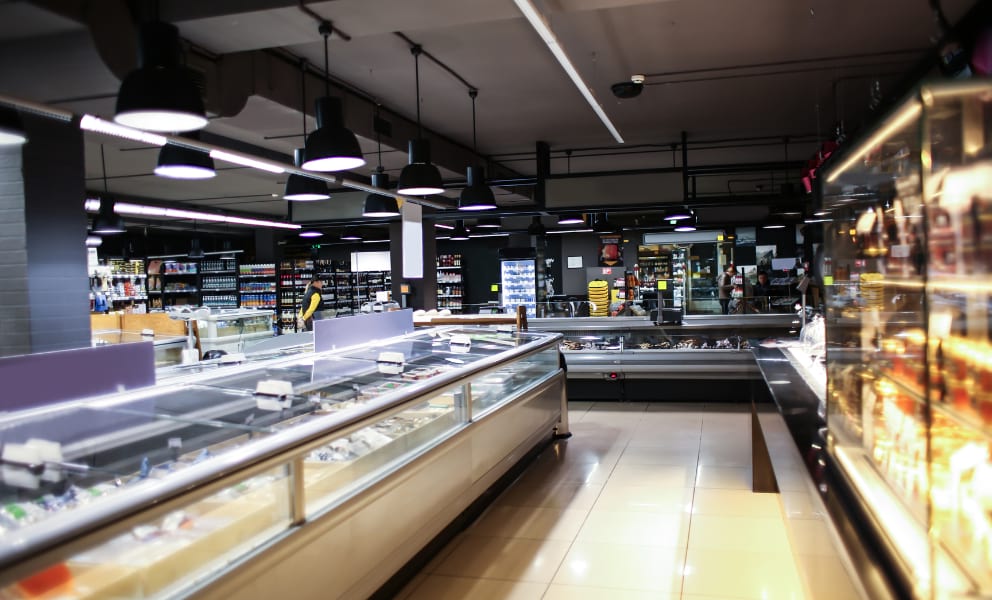
We have all been there. It’s a hot summer day, and you go into the supermarket to buy a few items for your backyard cookout—but as you move from produce to chips to the frozen aisles you become progressively more uncomfortable as the temperature and humidity within the space drastically swing. (Say it with me: shivering shoppers don’t shop long.)
Anyone tasked with managing retail grocery spaces knows that the pain of maintaining an optimal indoor environment goes far beyond comfort and can have a real impact on energy intensity and operational expenses. Balancing the ambient conditions around refrigerators and freezers, offsetting the heat produced by lights that illuminate produce, meat and dairy cases and maintaining the necessary humidity control to prevent food spoilage in pantry staples while ensuring frozen products in cases remain visible requires orchestrated synergy across multiple systems —likely being provided and serviced by multiple vendors.
Further complicating the situation are:
- An increased need for seamless omnichannel shopping—requiring more cold storage and readily accessible pick-up spaces
- Customers’ desires for healthier choices—which have a shorter shelf life and need tighter climate control to maintain freshness
- The impacts of inflation on already razor-thin margins
- Stakeholder expectations around meeting ESG goals—shifting the focus from not only reducing energy but working towards net zero carbon spaces
Fortunately, the answer lies in your HVAC-R system. Automating and connecting your building controls can provide you with the necessary data to visualize and take action to help reduce energy intensity, prolong equipment life and help reduce labor costs while ensuring maximum customer spend within your supermarket.
In this article we will highlight the three keys to integrating your heating, ventilation, air conditioning, lighting and refrigeration systems. The right building automation and management system can maximize the operational potential of your grocery store(s) while helping save time and money, reducing your environmental impact and protecting the integrity of your food products.
Step 1: Optimize building performance and streamline operational efficiencies with a connected building controller.
Just as our smartwatches, iPhones and online tv streaming services are constantly producing data about our habits, preferences and behaviors—buildings are a wealth of information about system performance, energy trends and potential warning signs of equipment failure. The key is understanding how to aggregate and interpret the information. In many grocery stores there are separate controls for the HVAC, lighting and food refrigeration systems. This can lead to disjointed and incomplete information along with the chaos of multi-vendor service management. When everyone is only focused on their part of the equation, a fix to one system can directly (and negatively) impact another. Turning up the lights to make sure the produce looks its best means the air-handler must work harder to maintain a temperature setpoint.
A powerful building automation system (BAS) can not only provide the HVAC-R control necessary to maintain comfort throughout a store, but can also be the source of centralization for all of your building systems. The Tracer SC+ from Trane uses BACnet open standard protocols and is built to seamlessly integrate with equipment from almost any manufacturer.
Coordinating all of the various isolated systems—like refrigeration racks, condensers, walk-ins, HVAC units and lighting—into a single point of management provides you with the assurance that nothing is being forgotten. Representative data on setpoints, trends, schedules and alarms can be easily accessed and managed. And, manual temperature logging is no longer necessary—a relief to anyone (everyone) who is short-staffed.
Step 2: Visualize building data to turn information into action.
With a foundation of centralized control through a BAS, a building management system (BMS) becomes the window into your systems. After nearly 50 years in the building controls business, we understand how your raw data can become actionable insights. This looks like streamlining access from each of your stores’ BAS into a single pane of glass for consolidated viewing. This can mean using intuitive and easy-to-set-up dashboards to give you real-time information about trends and energy usage so you can benchmark performance and identify anomalies. Standard and customized reports ensure that you can easily share the energy and cost savings you’re identifying.
Trane’s Tracer Ensemble is the industry leader when it comes to intuitive, feature-rich, purpose-built functionality. The web-based BMS assures you have access anytime, anywhere to system data and management—meaning the days of trying to troubleshoot or have local staff guess at what’s going on are over. You can identify which cost-prevention actions to take, where to reduce energy leakage, increase data transparency and reduce carbon-generating truck rolls no matter where you are —or, you can opt to have us manage it for you via remote access and our nationwide network of expert technicians.
Step 3: Maximize uptime and minimize disruption.
Information access through your BMS will almost certainly simplify your day-to-day operations. But when it comes to 24/7/365 monitoring, few can go it alone. Data-driven service not only gives you the peace of mind that your critical equipment and systems are always up and always on, but can also provide you with the expertise necessary to go beyond fix-on-fail and even preventative maintenance to proactive and predictive service and updates.
Consider the potential cost savings of preventing food spoilage by identifying and fixing an ailing compressor in your ice cream freezer before it goes down. Or imagine being able to predictably shave energy costs by optimizing the start/stop schedule of your rooftop units without sacrificing shopper comfort. Intelligent Services and Active Monitoring from Trane can deliver that and more. Using our experience from thousands of connected buildings on our platform, we can leverage data from across your portfolio for system-wide optimization through prescriptive algorithms, remote validation and even artificial intelligence to deliver continually improving results—allowing you to take advantage of the best optimization strategies and tactics without having to lift a finger.
So, back to you and your basket of cookout items. As a shopper, you know that the more comfortable a store is, the longer you’ll linger. As a store operator, you know that the more efficiently you can manage the microclimates around your building, the better your overall performance and profitability will be. Modern grocery stores need solutions that provide reliability, resiliency and redundancy. The right building automation and management solution can give you all three and more, allowing you to focus on what comes next.
Ice cream, anyone?
Retail Buildings
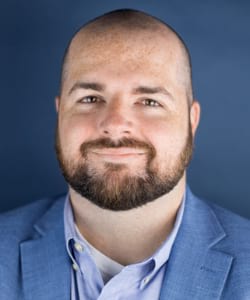
About the author
Ethan Kinsey, Sales Leader – Key Accounts
Ethan Kinsey is a sales leader for Trane’s Key Accounts team responsible for the innovation and growth in the Grocery store Vertical Market. In this role, Ethan leads a team of account executives focused on developing programs that provide consistent support of the execution of building expansion across the US and Canada as well as ongoing maintenance and optimization of their customer’s existing building footprint. Ethan has been with Trane since 2007 focused entirely on national program sales in the retail, commercial and industrial sectors. Ethan lives with his family in Sachse, TX and is a graduate of Texas A&M University.