Optimizing HVAC Maintenance When Runtime is Never the Same
August 12, 2020
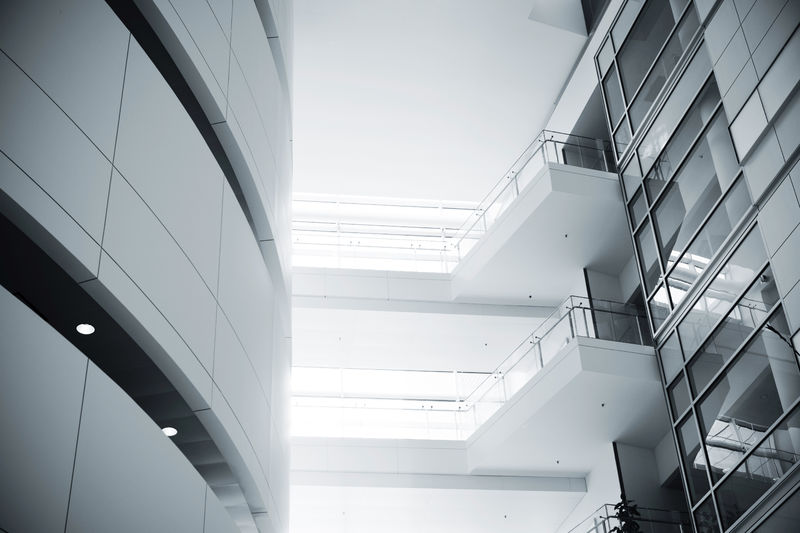
By integrating work orders with the building automation system (BAS), Trane’s work order management software makes it easy to order parts and perform maintenance based on actual equipment run time.
Facility professionals almost always defer to the calendar to schedule HVAC system maintenance. Equipment manufacturers publish calendar-based maintenance recommendations because it is a safe approach that is determined by the typical use or run time that would normally be expected during a set length of time.
But what is typical? It is difficult to know anymore.
Buildings that sit idle or are only partially open for weeks or months at a time don’t experience typical use. As businesses reopen, systems may need to run longer to accommodate new shifts and a staggered workforce. Building use patterns—and HVAC run time—may continue to fluctuate. Climate change is becoming a factor, too. More frequent and extreme heat waves put more strain on air conditioning systems. Warm, humid seasons are lasting longer.
The point is, actual system use has become more variable, and simply doing maintenance based on a pre-determined calendar date may not be the ideal approach.
Runtime data is tracked within building automation systems, but that source isn’t always easily accessible to the maintenance employees who could put it to practical use.
Trane’s new Work Order Management software is an optional feature of our Tracer® Ensemble® building management system. It automatically pulls in equipment runtime and displays the “hours remaining until maintenance” in an odometer format. Presenting the data on dashboards within the work order management interface that facility management teams review every day.
Our building experts help users set up customized, optimized maintenance schedules for changing air filters, cleaning and treating condenser and evaporator coils, checking refrigerant levels, inspecting bearings and more, making it easy for each site to optimize maintenance based on actual hours of use. And, since it is right there in the software that staff use daily, there’s little risk of letting things go for too long. Nor will you waste time and resources by prematurely replacing a perfectly good air filter or changing oil that is fine to use.