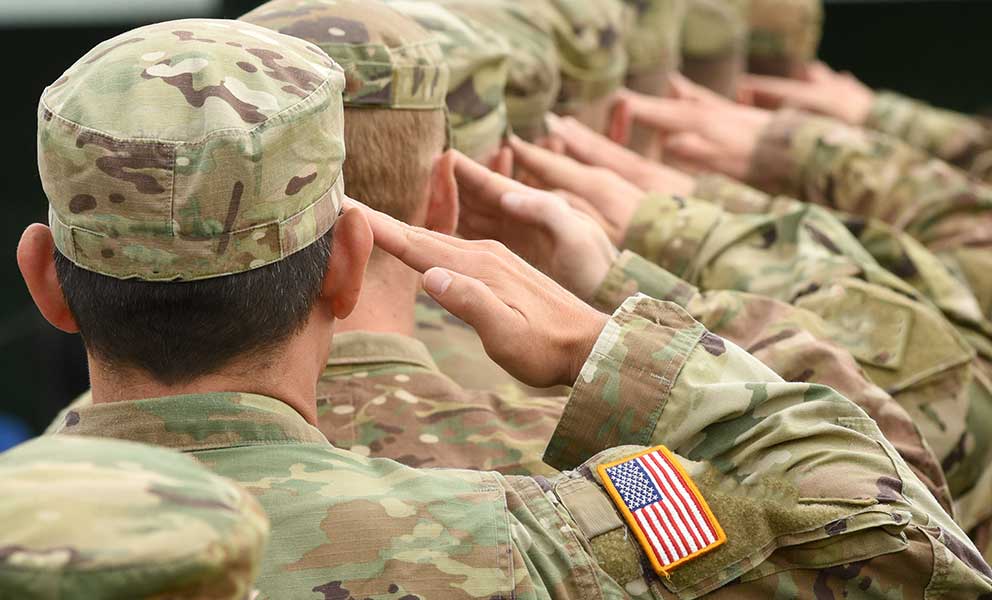
Customer Story
Fueling Progress: The US Air Force Launches its First LNG Plant
Industry: Federal Government
Topic: Innovation, Efficiency, Cost-Saving, Energy Services
- 20% reduction in energy waste across 679 buildings
- 70% of peak electrical demand now generated by renewables
- 20% reduction in the annual electrical load
- 14,619 mtCO2 annual reduction of greenhouse gas emissions
- $560 million project savings over the next 22 years
Challenge
Since the close of World War II the United States Air Force has maintained an extensive network of strategic air bases around the Pacific rim, at locations as far-flung as Alaska, Japan, South Korea, Singapore, and the islands of Hawaii, Wake Island, and Guam.
This year, one such base hosted a ribbon-cutting ceremony to recognize the commissioning of the first-ever liquefied natural gas (LNG) plant at a United States Air Force base. The event was held not only to celebrate the facility’s completion, but to recognize the potential of LNG technology to save cost, improve energy efficiency, and bolster Air Force mission resilience.
For years, the base had been searching for innovative new solutions to increase efficiency and reduce costs. The installation comprised nearly 700 different structures, a total of 8 million enclosed square feet. Buildings varied widely in size and function, from offices, warehouses, dormitories, recreation facilities and dining facilities, to mission-critical aircraft shelters and avionics repair facilities.
For all their diversity, however, all the buildings on base had a least one thing in common: they used too much energy. That was a serious problem in a part of the world where electricity cost 19 cents per kilowatt-hour (compared to an average 7 cents per kilowatt-hour in the US). The base needed to mitigate consumption, reduce heat loss, and bring costs under control, but without imperiling the steady energy supplies needed to ensure base operations.
“The project needed to leverage the existing infrastructure, but to also put in place a much more resilient installation,” said Jeff Rud, US Government energy solutions leader for federal clients. “It had to be able to adjust to either natural or manmade disruptions to energy security and allow operations to continue in the event of such a disruption.”
Solution
Trane performed an assessment of the base facilities, and shortly proposed a range of energy and facility improvement measures for the base, specifically tailored for the facility whose location was prone to severe weather and other disasters. Overall, the plan would emphasize not only efficiency but resiliency and increased redundancy.
The centerpiece of the initiative: a new liquified natural gas (LNG) facility to replace the base’s legacy fuel oil system. Once installed, the facility would allow for the decentralization of the legacy system and provide dual fuel capability for the base’s cogeneration plant. The LNG facility would be capable of producing six days' worth of fuel during peak heating season, thereby ensuring that the base could maintain operational continuity even in the face of a power disruption. The project also featured a renewable Solar PV (photovoltaic) energy system capable of providing more than 70% of the base’s peak demand.
Other improvements included modifications to the boiler plant, including new gas pipelines to decentralize the natural gas heating systems and reduce energy consumption and heat loss. Programmable thermostat controls were also added to the HVAC system in addition to infrared heating in forty of the base’s buildings. High-efficiency control valves were added to the chiller plant. To keep all the new infrastructure running smoothly into the future, Trane provided two full-time, on-site Sustainability Managers.
Results
All in all, the initiative has reduced energy waste by 20% across all the base’s 679 buildings. A total of 70% of peak electrical demand can now be generated by renewables. Efficiency measures have resulted in a 20% reduction in the annual electrical load. The new, cleaner source of fuel has reduced the base’s greenhouse gas emissions by 14,619 Metric Tons of CO2 equivalent annually. Projected savings over the next 22 years are $560 million.
The project was a collaboration between Trane, the Defense Logistics Agency, Tokyo Gas Engineering Solutions, and the 35th Fighter Wing, all working together under an Energy Savings Performance Contract (ESPC), which utilizes future energy savings to pay for building upgrades. The base’s journey towards energy efficiency and resiliency stands as a testament to the power of collaboration and innovation. It is first, but surely not the last, facility of its kind ever installed at a U.S. Air Force base.
Special thanks to the key stakeholders and project team: the 35th Civil Engineering Squadron, the 35th and 374th Contracting Squadrons, Defense Logistics Agency, AFCEC, AFIMSC, DOE and Tokyo Gas Engineering solutions.