Summary
The Hawaii Air National Guard, 154th Wing, shares the Hickam Air Force Base facilities with the Pacific Command. The base is located on 2,850 acres of land adjacent to Honolulu International Airport. To support the painting operation and maintenance of the Air National Guard F-22 Raptor jets, a new low observable/composite repair facility was built. The facility, consisting of a 17,500 sq ft hangar/paint booth and a 17,700 support building, features sophisticated mechanical systems for climate control for aircraft painting operations.
Challenge
The Hawaii Air National Guard outlined its criteria for a new hanger/paint booth and support building facility to maintain and repair its contingent of F-22 Raptor jets. The facility would need to meet complex, exacting temperature and humidity requirements in order to ensure process quality, and due to the nature of the operation, it must be explosion proof. In alignment with its environmental process objectives, the Air National Guard emphasized the need for energy efficiency in the facility design. Equipment reliability and redundancy were also required to ensure the building’s continuous operation. With F-22s waiting on the pad, a compressed design and construction schedule was developed.
Solution
Based on a ten-year relationship with the Air National Guard and its success on previous projects, Trane was contracted by the project’s mechanical engineer to provide equipment and direct digital (DDC) controls for the hangar support building. Trane’s experience and local presence, combined with the convenience and efficiency of using a central control system throughout the project, led the general contractor, Nan Inc., to contact Trane to also discuss a solution for the specified Programmable Logic Controller (PLC) paint booth controls.
Managing energy efficiency
The support building was designed and commissioned to meet US Green Building Council LEED (Leadership in Energy and Environmental Design) requirements. LEED promotes a whole-building approach to sustainability by recognizing performance in site development, water savings, energy efficiency, materials selection and indoor environmental quality. With energy efficiency an important element of the design, factory mounted direct digital controls (DDC) on Trane air handlers, fan coil units and variable air volume boxes were installed to meter and monitor energy use and volatile organic compound (VOC) levels. The controls are integrated into a Trane Tracer Summit® building automation system (BAS), which facility managers use to ensure system performance, manage energy use and perform daily tasks, such as scheduling, alarm management and data analysis.
Meeting complex specifications
Trane met with Nan Inc. to review the plans, detailed drawings and specifications for the PLC paint booths. The one-of-a-kind mirror image paint booth design, developed by the engineering firm, CH2M Hill, called for a temperature of 75 degrees +/- 2 degrees and humidity levels of 50 percent +/- 5 percent, with eighty-six feet per minute air flow across the bay, and a -0.01” pressure between the booth and the outside environment.
Trane consulted with Systems Integration Group, a software programming company they had worked with on previous projects. Familiar with Systems Integration Group’s expertise in PLC systems, Trane hired the company as a subcontractor to provide engineering and programming support, while Trane designed the overall concept and system integration.
Utilizing Trane’s relationship with GE, a fully-automated, easy-to-use GE 90-30 PLC was programmed to maintain the custom specifications, and designed with explosion-proof end devices. The booths are fully instrumented to control, monitor and maintain specific air flow across the booth floor and slightly negative pressure in the booth at all times during the painting mode. To maintain specifications, high-quality Trane Modular Climate Changer™ Air Handlers, designed for reliability and longevity, were installed, as well as custom heat wheel dehumidification units.
The booths have unoccupied, prep and purge modes that respond automatically to input from the PLC control panel or booth alarms. The GE PLC was integrated into the Tracer Summit® building automation system (BAS), allowing facility managers convenient access from a dedicated computer.
Results
Two custom designed paint booth hangars and a support facility were built to maintain the Hawaii Air National Guard’s fleet of F-22 Raptor jets. A $400,000 year-over-year savings is anticipated, compared to other paint booth hangars, due to an 80 percent recirculation of conditioned air and other design features. Trane controls and Tracer Summit BAS meet the strict standards set by project designers. The facility was awarded a LEED Gold Certification.
“Trane understood the complex requirements,” said James Zwiefel, Hawaii National Guard project manager. “And the open lines of communication between Trane, our designer and general contractor helped us more easily identify the right solutions and made the project go smoothly.”
”We’re looking at the possibility of implementing a webbased Tracer Summit Enterprise Server™ system to tie all of the Air National Guard Tracer Summit sites together," said John Yap, Hawaii National Guard building maintenance supervisor. "One system would make it more convenient.”
About Hawaii Air National Guard
The Hawaii Air National Guard’s low observable/composite repair facility includes two custom designed, mirror image paint booths.
The Air National Guard paint booths are fully instrumented to control, monitor and maintain exacting temperature and humidity requirements.
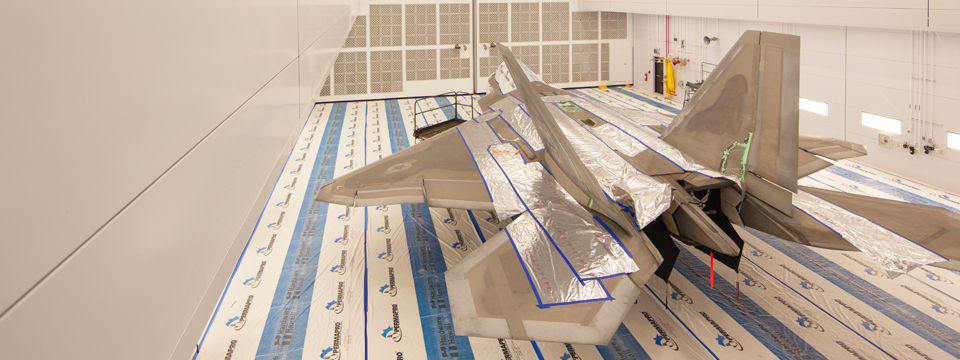