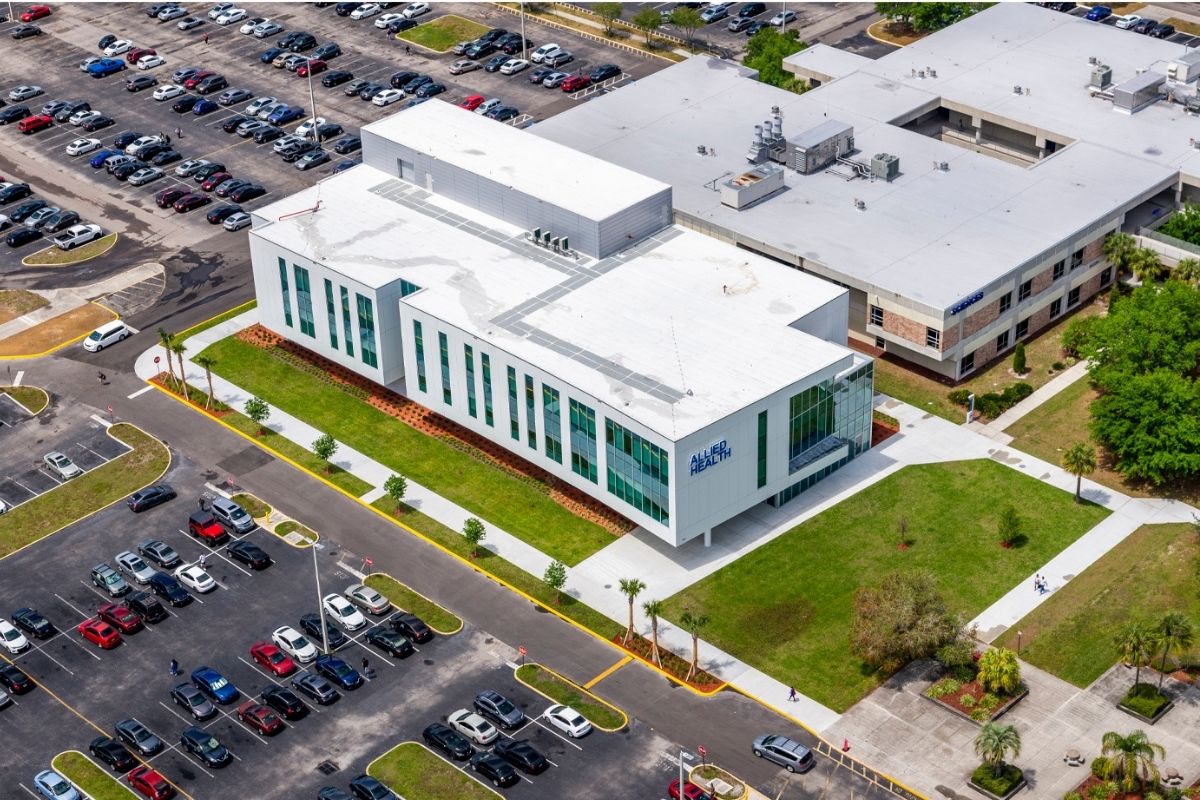
Customer Story
Hillsborough Community College
Location: Florida
Industry: Higher Education
Products Used: Chillers, Controls
Services Used: Energy Supply, Energy Analysis & Monitoring
Topic: Efficiency, Sustainability, IEQ
Challenge
Leaders at Florida’s Hillsborough Community College (HCC) faced multiple infrastructure challenges across the school’s 61 buildings and 1.8 million square feet of space. Administrators wanted to reduce the College’s energy footprint, optimize aging and outdated heating ventilation and air conditioning (HVAC) systems to lower high energy and operational costs. Leaders also wanted to improve indoor environmental quality (IEQ) and building comfort. They sought a data-driven roadmap for change and innovative solutions to align with the College’s culture of sustainability.
Specific challenges at the College’s five campuses and district administration building included replacing obsolete systems and standardizing outdated, unreliable building controls representing a mix of manufacturers.
Approach
Given the depth and breadth of the daunting need and based on a long-standing relationship with Trane, administrators turned to the energy service company to help develop a comprehensive, methodical approach to upgrading the College’s facilities.
Holistic approach, five-year plan
Trane took a holistic approach to the project, partnering with HCC leaders to develop a five-year asset-management improvement plan that incorporated a data-driven approach. The plan addressed the need to replace aging and obsolete systems for greater efficiency, embrace current technology, utilize cloud platforms and standardize and upgrade controls.
The team started by gathering baseline data for energy bills and water consumption on a buildingby- building basis. This analytical process informed decision making, enabling them to identify and prioritize the most critical replacements.
Standardized and upgraded controls
Based on the comprehensive plan, the project team undertook an extensive effort to replace and standardize controls. Standardizing controls enabled system performance visibility as well as building-wide performance insights.
The team implemented Tracer® SC building automation systems as part of the controls upgrade and standardization process. Tracer SC acts as a system functions and network manager for all individual HVAC systems, giving facility managers secure HVAC system access remotely via mobile devices such as tablets or smart phones. Using Tracer SC, facility managers can establish scheduling, change set points, and manage energy use.
The facilities team also gained an enterprise-wide view of systems with Tracer® Ensemble®, a web-based building management system (BMS) that dramatically simplifies the complex requirements of managing and operating multiple facilities. Accessible from most PCs, tablets, and smartphones, Tracer Ensemble gives the team immediate access to building systems from virtually any location, allowing them to maintain comfortable, consistent conditions across their campuses.
Both Tracer solutions enabled improved ease of operation, faster response times and high reliability, streamlining building management and enhancing facilities staff productivity.
Energy Analysis and Monitoring
The College also implemented Energy Analysis and Monitoring from Trane which uses intelligent tools to monitor, track, predict and optimize operation. This offering enables smarter building management: it uses advanced monitoring and analytics to gather data, helps identify opportunities for improvement, prioritizes the work, implements the solutions and validates the results.
Based on the data these solutions provided the project team identified the next phase of energy conservation improvement measures and tackled those on a building-by-building basis, addressing the greatest needs first based on the story the data told.
New systems
Updated energy conservation measures implemented included chillers variable air volume systems, air handling units and more. In some cases, thermal energy storage was implemented to help reduce energy costs associated with comfort cooling by shifting equipment operation from high- to low-cost times of day.
Preventative maintenance
The project team also developed and launched a preventative maintenance effort as part of the five-year plan. Data and analytics from the standardized, connected controls provided a targeted and holistic approach to help inform preventative maintenance undertaken with Trane. The preventative maintenance agreement helps ensure that upgraded systems keep running at optimal performance.
Results
While upgrades continue, HCC has already saved nearly $1.8 million in energy costs and nearly 23 million kWh over the past five years. The College has improved IEQ throughout its facilities while reducing its environmental footprint.
Through its collaboration with Trane, HCC upgraded key infrastructure, installing more efficient solutions, upgrading obsolete controls systems while embracing the benefits of the latest software analytics technologies. Upgraded and standardized controls have increased security, improved staff productivity and facilitated better building, campus and enterprise management. Trane Intelligent Services® solutions enabled a data-driven approach to informed decision-making allowing the team to optimize both building comfort and wellness, while expanding equipment life expectancy and reducing energy costs.