Project Highlights
Location: Charlotte, North Carolina
Industry: Commercial Real Estate
Products Used: Chillers, Air Handling, Controls
Services Used: Energy Analysis & Monitoring, Rental Services, Upgrading
Climate: Humid & Hot
Topic: Sustainability, Efficiency, Cost-Saving, Optimal Comfort
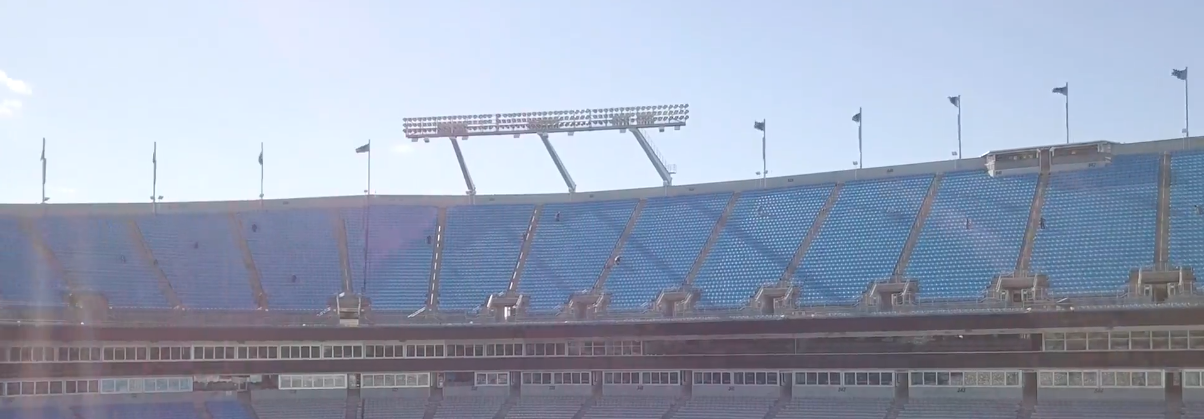
The Challenge: Aging HVAC Equipment
Faced with the need for additional cooling capacity, high energy costs, and an aging infrastructure, Bank of America Stadium, home of the Carolina Panthers, was also challenged by a short off-season. With events already scheduled and tickets sold, it was critical that necessary upgrades adhere to strict deadlines to provide comfort for stadium guests and alleviate the inconvenience and financial burden of cancellations. In addition, the stadium had the added challenge of needing to maintain 1,000 tons of cooling throughout construction to keep onsite football players and administrative personnel comfortable.
“After one of our summer renovations, we realized that our chiller capacity was no longer capable of carrying the building,” said Matthew Getz, Facilities Manager, Carolina Panthers. “Our plant was undersized, reliability was an issue, and our 20-year-old original equipment was using a lot of energy.”
“About 30 minutes prior to kick-off, fans arrive and put a huge load on the plant. On hot days during early-season games, the chillers would try to maintain temperature, but couldn’t keep up,” said Shane Walden, Mechanical Systems Manager, Carolina Panthers. “We’d have to bring in a 500-ton rental chiller for supplemental cooling to get us through.”
The Solution: Holistic System Updates
Based on a long-term service and maintenance relationship at the facility, Trane’s suggested design solutions, and its ability to complete the project within the tight timelines, the Carolina Panthers stadium operations team selected the company for its needed HVAC and controls upgrades. Trane and the stadium facilities team worked hand-in-hand to develop the project scope, from chiller plant design and equipment selection, through execution, project management and commissioning. “We provided an outline to the project,” said Getz. “Trane provided not only solutions that fit our needs, but also brought new ideas to the table.”
Increasing cooling capacity
Trane worked with the local utility to complete an energy analysis of the facility. The study validated the need for increased capacity, and calculated rebates the Carolina Panthers would receive when three new 1000-ton Trane CenTraVac® chillers replaced the aging 750-ton chillers. The more efficient chillers fit within the same footprint, without changing any of the electrical requirements. Trane Rental Solutions provided rental chillers for cooling until the new equipment was up and running.
Improving efficiency
Trane converted the plant from a primary-secondary-tertiary piping system to a variable-flow-primary plus booster pump system. This reduced the total number of pumps and lowered energy use, while improving comfort. In addition, hydronic redundancy was enhanced by reconfiguring the three pumps to allow any to run with any chiller, plus bypass piping was added to allow for primary pumping during low load conditions. These upgrades allow the chilled water to flow through the building without restriction. The turnkey project also included installation of a Trane® Performance Climate Changer® air handling unit, and variable frequency drives (VFDs) on three chilled water pumps, three cooling tower fans and eight quad pumps.
Integrating technologies for convenient control and improved comfort
Nine building control units were replaced with five Tracer® SC building automation systems (BAS) and four communication bridges. A Tracer® Ensemble™ building management system provides an enterprise view of the entire facility and web interface, allowing facility managers to conveniently access and control systems from anywhere using a mobile device. The chiller plant controls were upgraded to Tracer UC600, and existing controllers were integrated into the new system. Extensive programming was completed to support plant configuration changes and provide automation to manual tasks. The stadium uses the BAS for scheduling, to optimize plant control, fine tune the temperature in each individual suite, and control comfort for building occupancy levels that can vary from 500 people one day to 75,000 the next. With the BAS, facility managers can remotely shut equipment of, bypass pumps not required, or start a chiller to bring the temperature down quickly.
Ensuring systems are running at their best
Training sessions for stadium personnel were held at Trane’s Charlotte Training Office, and on-site at the chiller plant. The Trane turnkey solution included on-site support for the first three events held at the stadium to thwart obstacles. Ongoing, quarterly chiller and controls maintenance by Trane professional technicians ensures the systems are running at their best.
The Results: Improved Capacity, Savings and Comfort
For the Carolina Panthers' stadium renovations, the operations team partnered with Trane to complete chiller plant and BAS upgrades, while meeting deadlines and keeping the facility up and operating throughout construction. The project increased reliability and capacity, keeping players and fans comfortable during Carolina Panthers games, while improving efficiency and reducing energy consumption. The projected savings resulting from the upgrades is $80,000 annually. Trane also helped the Carolina Panthers apply for energy rebates from the local utility company.
“With the increased capacity, we can now carry the load on hot summer games without supplemental cooling,” said Getz. “We had tight parameters and a tight timeline. Trane was able to make it happen.”