6 ways for indoor agriculture to grow sustainability
November 17, 2021
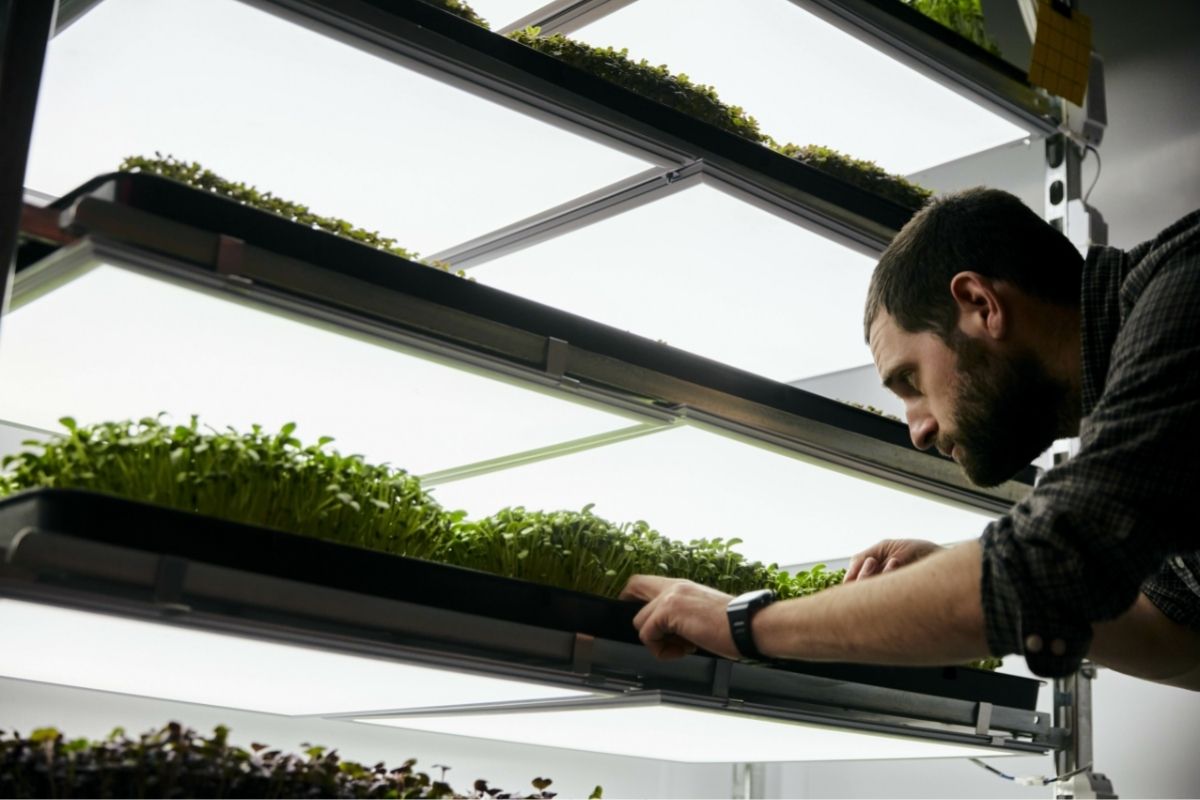
Indoor agriculture operations are sprouting up in surprising places, fueled by rising global food demand and legalized cannabis. It’s a growth industry with a big appetite for energy.
Precisely maintained indoor environments make indoor growing operations highly efficient. They consume up to 95% less water, use less fertilizer and pesticide and are hundreds of times more productive per square foot compared to traditional farming methods. And growers don’t need to worry about Mother Nature spoiling the harvest.1
But the rapid growth of controlled environment agriculture (CEA) can challenge local electrical infrastructure because of the significant energy required to maintain indoor lighting and climate conditions 24 hours a day. In fact, indoor ag operations can exceed even power-hungry data centers in energy intensity per square foot.2 Policymakers and regulators at all levels are starting to take note, and experts believe efficiency standards are only a matter of time for indoor growers.3
Building efficiency and sustainability into an indoor growing operation can help growers stay ahead of the issue, and deploying the right technology is where it all starts. Whether it’s a multi-million-dollar legally licensed cannabis cultivation facility or a co-op urban vertical farm, a technology-based approach to indoor growing can help optimize sustainability and crop yield and quality.
Maintaining an energy efficient and consistent indoor growing climate is a technical challenge. There are horror stories out there—water in buildings, fungus and mold buildup in grow rooms, mis-applied or wrongly-installed equipment that leads to continuous headaches and massive crop loss. Off-the-shelf or ‘I know a guy’ solutions can be risky and expensive mistakes, which could result in dire outcomes for years.
Here are 6 ways vertical farms and legally licensed commercial cannabis grow rooms can become more energy efficient and sustainable:
1. It starts with a plan.
A commercial grow room is a complex environment that requires precision systems calibrated to maintain specific and even proprietary growing conditions. Accuracy and reliability are essential for grow room success. HVAC experts can provide the proper up-front design and planning to ensure the system meets a grower’s unique operational needs, whether for an existing grow room operation or in a new or retrofitted building.
2. Select equipment designed for the task
HVAC for indoor agriculture is not one-size-fits-all. There are many kinds of HVAC systems available, from packaged rooftop units to large air- or water-cooled chillers, all available in a broad range of features and capacities to support operations of any size. Factors such as air movement, irrigation rates, plant volume in grow rooms, lighting wattage, desired temperature and humidity levels – even room dimensions – can be important inputs to ensure you choose the right HVAC solution for your crop needs.
3. Make sure it’s scalable
Controlled Environment Agriculture (CEA) is expanding at a fast rate. Correct sizing of Indoor Agriculture HVAC equipment is tied to commercial grow room needs, but those needs change as an operation grows. It can be tempting to stretch an existing system’s capabilities to keep pace – just add a few floor humidifiers, for example. But that just adds more heat to be removed and may jeopardize the ability of a system to maintain accurate temperature and humidity levels. Choose an HVAC solution with scalability in mind, so the indoor climate is consistently maintained as production capacity increases.
4. Use energy efficient technology – especially grow lights
Grow lights are the operation’s most significant energy consumer. Consider avoiding the energy-intensive options, such as high-pressure sodium and high-intensity discharge lights, in favor of LED grow lights. LED technology generates less heat, which reduces cooling costs, and emits greater luminosity per watt, which reduces electricity consumption. They also have variable spectra available and can be easily networked into a building automation system (BAS) for a single point of control.
5. Use automation to drive efficiency and sustainability
Electricity costs vary by time of day, and it’s most expensive when demand is highest during daylight hours. Automation simplifies scheduling of grow room operations to take advantage of off-peak hours and night-time use, when electricity demand and rates are lowest. Automating this process takes the burden off staff and ensures consistency. Tying all key systems into a BAS streamlines overall management of operations and allows growers to monitor and manage the system remotely at any time.
6. Partner with an HVAC expert
Highly technical operations go by many names, from indoor agriculture, vertical farming, controlled environment agriculture (CEA), and more—they all rely on sophisticated systems, and dependable uptime is paramount for success. Choose an HVAC partner that supports growers throughout system design, installation, system use and expansion. A service agreement can not only ensure key HVAC systems are properly maintained to provide maximum uptime—protecting the investment and future key infrastructure—but also provide critical peace of mind. Look for partners who can provide 24/7 remote monitoring and mitigation to manage service costs when possible but have the capacity for on-site support when critical issues arise.
1 (Electric Power Research Institute (EPRI), January 26, 2021: “Can Indoor Agriculture Help Feed a Growing World?”)
2 (GreenBiz, March 6, 2020: “Microgrids, indoor agriculture go together like peas and carrots”)
3 (Cannabis Science and Technology, June 22, 2021: “Is Carbon-Neutral Cannabis Possible?”)