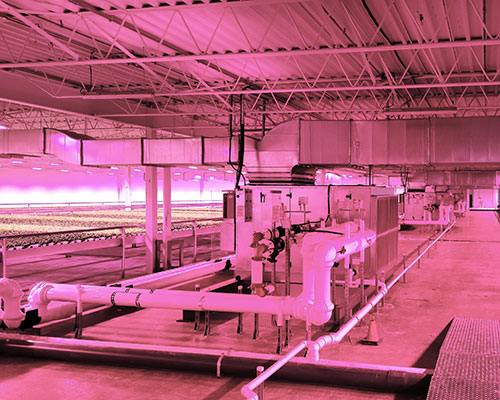
Due to Canada's short growing seasons, agriculture has long been difficult. Much of the country's winter produce is imported from California. However, there's been a movement in Quebec and other provinces to embrace year-round farming.
Lufa Farms is on a mission to deliver sustainable, locally-produced vegetables – particularly in winter. Initially, the company built greenhouses on warehouse roofs, undeveloped territory and inexpensive to lease. Theoretically, heat loss from the buildings would help support crops, but theory doesn't always pan out.
"Lufa Farms found there isn't as much heat loss through the roof as they thought," said Jean-François Vallée, an engineer and Navada's Vice President of Development. "They needed another plan."
In conversations with Lufa Farm's president, Mohamed Hage, Vallée suggested moving the entire operation indoors. Hage was skeptical. Indoor farming looked incredibly expensive. However, other companies were developing these farms around Quebec, and eventually Hage agreed. Navada jumped on the project.
Once a Retail Store, Now a Farm
Indoor farming offers some advantages over the traditional variety. Because the lighting, climate and other factors are precisely controlled, the output can be more reliable and often higher quality.
"We build custom, artificial environments for the plants," said Vallée. "And because everything is artificial, we can provide better consistency than nature. The growing cycle is like a metronome."
Lufa's first indoor project was built in a former retail store, which they share with other tenants. The project was complicated because the structure was built in the 1970s, with different codes, and the budget was limited.
While many indoor farms stack crops vertically, Lufa took a horizontal approach, the same way they'd worked in greenhouses. The company uses a rotating growing system, like a conveyor belt. On one side of a long table, crops are planted in large pallets. As the plants grow, mechanical arms move the pallets forward on the table, and new pallets are added behind them. This process continues until mature crops emerge on the far side of the table for harvest.
A Precisely Controlled Environment

What indoor farms lose in sunlight, wind, and rain, they gain in precise environmental control and sustainability. Trane equipment is helping Lufa become carbon neutral and reduce water consumption. Also, because they are so well contained, indoor farms don't need pesticides, eliminating the runoff that can damage watersheds.
Still, creating a farm in a 1970s-era retail building was challenging. One concern was condensation on steel beams. Rusty droplets could contaminate crops. The answer was to adjust temperature, humidity, airflow, and other factors to control it.
"We needed to maintain a certain airflow all around the facility," said Vallée, "not too high and not too low. We were installing new equipment, two Trane® water-cooled helical rotary chillers, which could do whatever we needed them to do. That made it relatively easy."
Controlling water use helps reduce costs and boosts sustainability, but it's also good for the community. Lufa Farms' downstairs neighbor keeps a lot of cardboard stock, and any leakage would be disastrous.
"We recover all the water and reuse it," said Vallée. "We remove humidity from the air, put it in our basin, and then reinject it onto the plants, like a circle. We don't waste water at all. Also, when we're cooling the vegetables in one part of the facility, we're not throwing the heat out through the roof. We're reclaiming that energy and diverting it into other systems that may heat or dehumidify other areas."
The heat recovery is efficient, makes the government happy, and qualifies Lufa for generous grants to help defray costs. But even that solution was not completely straightforward. Because of weight concerns in the old building, Navada built a separate structure underneath the chillers to distribute their weight more broadly.
Navada is investigating different ways to use equipment and won't rely on popular wisdom to inform their choices. As a result, they're testing new approaches, like pushing chillers at higher temperatures, to squeeze maximum efficiency from their systems.
"We're trying to make things work and looking at the overall benefits of doing something a little different," said Vallée. "I'm always telling my team that we're doing financial engineering, and that means coming up with the most moneywise, efficient systems for each application."